Injection molding သည် ပလပ်စတစ် အစိတ်အပိုင်းများနှင့် ထုတ်ကုန်အမျိုးမျိုးကို ထုတ်လုပ်ရန်အတွက် တွင်ကျယ်စွာ အသုံးပြုသော ကုန်ထုတ်လုပ်မှု လုပ်ငန်းစဉ်တစ်ခုဖြစ်သည်။စွယ်စုံရနှင့် ထိရောက်မှုရှိသော ဤလုပ်ငန်းစဉ်သည် မြင့်မားသောတိကျမှုနှင့် ထပ်တလဲလဲနိုင်မှုဖြင့် ရှုပ်ထွေးသောပုံစံများနှင့် ရှုပ်ထွေးသောအစိတ်အပိုင်းများကို အစုလိုက်အပြုံလိုက်ထုတ်လုပ်နိုင်စေပါသည်။ဆေးထိုးပုံသွင်းခြင်းလုပ်ငန်းစဉ်တွင် အဆင့်များစွာပါဝင်ပြီး အရည်အသွေးမြင့် အစိတ်အပိုင်းများ ထုတ်လုပ်မှုကို သေချာစေရန်အတွက် တစ်ခုစီတွင် အရေးကြီးပါသည်။ဆေးထိုးခြင်းလုပ်ငန်းကို အဆင့်ဆင့်လေ့လာကြည့်ရအောင်။
အဆင့် 1: ဆေးထိုးမှိုဒီဇိုင်း
ဆေးထိုးပုံသွင်းခြင်း၏ ပထမအဆင့်မှာ မှိုကို ဒီဇိုင်းထုတ်ခြင်း ဖြစ်သည်။မှိုဒီဇိုင်းသည် မူကြမ်းထောင့်၊ နံရံအထူတူညီမှု၊ ဂိတ်ပေါက်နှင့် ထုတ်ပယ်သည့် ပင်နံပါတ်တည်နေရာများနှင့် အကောင်းဆုံးသော အစိတ်အပိုင်း အရည်အသွေးနှင့် ထုတ်လုပ်နိုင်စွမ်းကို သေချာစေရန် အအေးခံချန်နယ်နေရာချထားခြင်း စသည့်အချက်များကို ထည့်သွင်းစဉ်းစားရပါမည်။မှိုဒီဇိုင်းသည် နောက်ဆုံးအပိုင်း၏ ဘက်မလိုက်တိကျမှု၊ မျက်နှာပြင်အချောထည်နှင့် တည်ဆောက်ပုံဆိုင်ရာ ခိုင်မာမှုကို ဆုံးဖြတ်ရာတွင် အရေးကြီးပါသည်။မှိုဒီဇိုင်းကို အပြီးသတ်ပြီးသည်နှင့် ၎င်းကို တိကျသော စက်ပိုင်းဆိုင်ရာ လုပ်ငန်းစဉ်များကို အသုံးပြု၍ ထုတ်လုပ်ပါသည်။
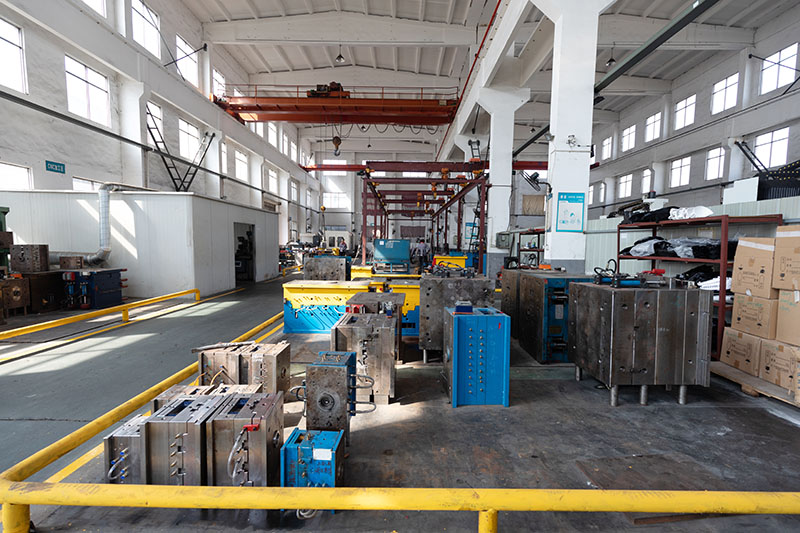
အဆင့် 2- ပစ္စည်းပြင်ဆင်ခြင်း။
ကုန်ကြမ်းများကို အများအားဖြင့် အစေ့အဆန်များ သို့မဟုတ် granules ပုံစံဖြင့် နောက်ဆုံးထုတ်ကုန်၏ သီးခြားလိုအပ်ချက်များအပေါ် အခြေခံ၍ ဂရုတစိုက်ရွေးချယ်ပါသည်။အချောထည်အစိတ်အပိုင်းသည် လိုချင်သောဂုဏ်သတ္တိများရှိကြောင်း သေချာစေရန် အရည်ပျော်စီးဆင်းမှု၊ viscosity၊ ကျုံ့မှုနှင့် ခိုင်ခံ့မှုကဲ့သို့သော ပစ္စည်းဂုဏ်သတ္တိများကို ထည့်သွင်းစဉ်းစားရန် အရေးကြီးပါသည်။ထို့အပြင်၊ ရောင်ခြယ်ပစ္စည်းများ၊ ဖြည့်စွက်ပစ္စည်းများ သို့မဟုတ် အားဖြည့်အမျှင်များကို အလိုရှိသော စွမ်းဆောင်ရည်နှင့် အသွင်အပြင်ရရှိစေရန် ဤအဆင့်တွင် ပစ္စည်းရောစပ်မှုတွင် ထည့်သွင်းနိုင်သည်။
အဆင့် 3: Clamping နှင့် Injection
ပစ္စည်းနှင့် မှိုများကို ပြင်ဆင်ပြီးသည်နှင့်၊ ကုပ်ခြင်းနှင့် ဆေးထိုးခြင်း အဆင့်များ စတင်ပါသည်။မှို၏နှစ်ခြမ်းကို အပိတ်အပေါက်တစ်ခုအဖြစ် ဖန်တီးရန်အတွက် ဆေးထိုးပုံသွင်းစက်အတွင်းတွင် လုံလုံခြုံခြုံ ချိတ်ထားသည်။ထို့နောက် ပလပ်စတစ်အစေးကို တိကျသောအပူချိန်တစ်ခုတွင် အပူပေးပြီး ဖိအားမြင့်သောပုံစံခွက်ထဲသို့ ထိုးသွင်းပါ။သွန်းသောပစ္စည်းသည် အပေါက်အတွင်း ပြည့်သွားသည်နှင့်အမျှ၊ ၎င်းသည် မှိုဖွဲ့စည်းမှုပုံစံ၏ ပုံသဏ္ဍာန်ပေါ် မူတည်သည်။ဆေးထိုးသည့်အဆင့်သည် ပျက်ပြယ်သွားခြင်း၊ နစ်မြုပ်နေသော အမှတ်အသားများ သို့မဟုတ် ကွဲထွက်ခြင်းကဲ့သို့သော ချို့ယွင်းချက်များကို ရှောင်ရှားရန် ဆေးထိုးခြင်းအမြန်နှုန်း၊ ဖိအားနှင့် အအေးခံချိန်ကဲ့သို့သော လုပ်ငန်းစဉ်ဘောင်များကို ဂရုတစိုက်ထိန်းချုပ်ရန် လိုအပ်သည်။
အဆင့် 4: အအေးခံခြင်းနှင့် ခိုင်မာစေခြင်း။
အပေါက်ပြည့်သွားသည်နှင့် သွန်းသောပလပ်စတစ်သည် မှိုအတွင်းတွင် အေးပြီး ခိုင်မာသွားနိုင်သည်။သင့်လျော်သောအအေးပေးခြင်းသည် လိုအပ်သောအစိတ်အပိုင်းစွမ်းဆောင်ရည်ကိုရရှိရန်နှင့် လည်ပတ်ချိန်များကိုလျှော့ချရန်အတွက် အရေးကြီးပါသည်။မှိုဒီဇိုင်းသည် ပစ္စည်း၏ အပူကို လျင်မြန်စွာနှင့် အညီအမျှ ပြေပျောက်စေရန် ကူညီပေးသော အအေးခံလမ်းကြောင်းများ ပါ၀င်ပြီး တစ်သမတ်တည်း အစိတ်အပိုင်း အရည်အသွေးနှင့် အတိုင်းအတာ တည်ငြိမ်မှုကို သေချာစေသည်။အအေးခံခြင်းလုပ်ငန်းစဉ်ကို စောင့်ကြည့်ခြင်းနှင့် ပိုမိုကောင်းမွန်အောင်ပြုလုပ်ခြင်းသည် အစိတ်အပိုင်းပုံပျက်ခြင်း သို့မဟုတ် အတွင်းပိုင်းဖိစီးမှုများကဲ့သို့သော ပြဿနာများကို တားဆီးရန်အတွက် အရေးကြီးသောအချက်မှာ ကုန်ချောထုတ်ကုန်၏ ကြံ့ခိုင်မှုကို ထိခိုက်စေနိုင်ပါသည်။
အဆင့် 5- ထုတ်ပယ်ခြင်းနှင့် အစိတ်အပိုင်းများ
ဖယ်ရှားခြင်း ပလပ်စတစ်ကို အပြည့်အဝအအေးခံပြီး ခိုင်မာသွားပြီးနောက်၊ မှိုပွင့်သည်နှင့် အသစ်ဖွဲ့စည်းထားသော အစိတ်အပိုင်းကို အပေါက်မှ ထုတ်ပစ်လိုက်သည်။မှိုတွင်တည်ဆောက်ထားသော ejector pin သို့မဟုတ် ယန္တရားတစ်ခုကို အသက်သွင်းခြင်းသည် အစိတ်အပိုင်းကို တွန်းထုတ်ပြီး ၎င်းကို ကိရိယာမျက်နှာပြင်မှ ထုတ်လွှတ်သည်။အထူးသဖြင့် ရှုပ်ထွေးသော ဂျီသြမေတြီများ သို့မဟုတ် နံရံပါးလွှာသော အစိတ်အပိုင်းများနှင့် အစိတ်အပိုင်း သို့မဟုတ် မှိုပျက်စီးမှုကို ကာကွယ်ရန်အတွက် ထုတ်လွှတ်သည့်လုပ်ငန်းစဉ်ကို ဂရုတစိုက် ထည့်သွင်းစဉ်းစားရပါမည်။အစိတ်အပိုင်းများကို ထုတ်လွှတ်ခြင်းနှင့် ဖယ်ရှားခြင်းတို့ကို အရှိန်မြှင့်ရန် အလိုအလျောက်စနစ်များကို အကောင်အထည်ဖော်နိုင်ပြီး အလုံးစုံထုတ်လုပ်မှု ထိရောက်မှုကို မြှင့်တင်ပေးနိုင်သည်။
အဆင့် 6- ချုံ့ပြီး အပြီးသတ်ပါ။
တစ်စိတ်တစ်ပိုင်းကို ထုတ်ပစ်လိုက်သည်နှင့်အမျှ ပိုလျှံနေသော အရာများ (burrs ဟုခေါ်သည်) ကို အပိုင်းမှ ဖြတ်တောက်ခြင်း သို့မဟုတ် ဖယ်ရှားခြင်း ခံရသည်။၎င်းတွင် နောက်ဆုံးအပိုင်း သတ်မှတ်ချက်များရရှိရန် လိုအပ်သော အခြားအချောသတ်ခြင်းလုပ်ငန်းစဉ်များဖြစ်သည့် deburring၊ gate ဖယ်ရှားခြင်း သို့မဟုတ် အခြားသော ပြီးစီးမှုလုပ်ငန်းစဉ်များကဲ့သို့သော ဆင့်ပွားလုပ်ဆောင်မှုများ ပါဝင်နိုင်သည်။မျက်နှာပြင်မစုံလင်မှု သို့မဟုတ် ရှေ့နောက်မညီမှုများကို ကိုင်တွယ်ဖြေရှင်းပြီး အသုံးချမှုလိုအပ်ချက်များပေါ်မူတည်၍ အစိတ်အပိုင်းသည် စက်ယန္တရား၊ ဂဟေဆော်ခြင်း သို့မဟုတ် တပ်ဆင်ခြင်းကဲ့သို့သော ထပ်လောင်းလုပ်ဆောင်မှုများကို လက်ခံရရှိနိုင်ပါသည်။
အဆင့် 7- အရည်အသွေးထိန်းချုပ်ရေးနှင့် စမ်းသပ်ခြင်း။
ဆေးထိုးပုံသွင်းခြင်း လုပ်ငန်းစဉ်တစ်လျှောက် အရည်အသွေးမြင့် အစိတ်အပိုင်းများ ထုတ်လုပ်မှုကို သေချာစေရန် အရည်အသွေးထိန်းချုပ်မှု အစီအမံများကို အကောင်အထည်ဖော်ဆောင်ရွက်ပါသည်။၎င်းတွင် လုပ်ငန်းစဉ်ဘောင်များကို စောင့်ကြည့်ထိန်းချုပ်ခြင်း၊ ချို့ယွင်းချက်များအတွက် အစိတ်အပိုင်းများကို စစ်ဆေးခြင်းနှင့် အတိုင်းအတာတိကျမှု၊ ခိုင်ခံ့မှုနှင့် အခြားဂုဏ်သတ္တိများကို အကဲဖြတ်ရန် အမျိုးမျိုးသောစမ်းသပ်မှုများ ပြုလုပ်ခြင်းတို့ ပါဝင်နိုင်သည်။
အချုပ်အားဖြင့်ဆိုရသော် ဆေးထိုးပုံသွင်းခြင်းလုပ်ငန်းစဉ်သည် ထူးခြားသောတိကျမှုနှင့် ထိရောက်မှုရှိသော ပလပ်စတစ်အစိတ်အပိုင်းများနှင့် ထုတ်ကုန်အများအပြားကို ထုတ်လုပ်နိုင်သည့် ရှုပ်ထွေးပြီး စွယ်စုံသုံးကုန်ထုတ်လုပ်မှုနည်းပညာတစ်ခုဖြစ်သည်။လုပ်ငန်းစဉ်အတွင်း အဆင့်တိုင်း၊ ပစ္စည်းပြင်ဆင်ခြင်းနှင့် မှိုဒီဇိုင်းမှ အအေးခံခြင်း၊ ထုတ်လွှတ်ခြင်းနှင့် အရည်အသွေးထိန်းချုပ်ခြင်းအထိ၊ အကောင်းဆုံးရလဒ်များရရှိရန် အသေးစိတ်နှင့် ကျွမ်းကျင်မှုများကို ဂရုတစိုက်အာရုံစိုက်ရန် လိုအပ်ပါသည်။ဆေးထိုးပုံသွင်းခြင်းလုပ်ငန်းစဥ်၏ အဆင့်တိုင်းကို နားလည်ပြီး ပိုမိုကောင်းမွန်အောင်ပြုလုပ်ခြင်းဖြင့်၊ ထုတ်လုပ်သူများသည် မတူကွဲပြားသောစက်မှုလုပ်ငန်းနှင့် အသုံးချမှုလိုအပ်ချက်များကိုဖြည့်ဆည်းရန်အတွက် အရည်အသွေးမြင့်၊ ကုန်ကျစရိတ်သက်သာသော အစိတ်အပိုင်းများကို တသမတ်တည်း ပေးပို့နိုင်ပါသည်။
တင်ချိန်- ဒီဇင်ဘာ ၁၂-၂၀၂၃