قالب گیری تزریقی یک فرآیند تولیدی پرکاربرد است که برای تولید انواع قطعات و محصولات پلاستیکی استفاده می شود.این فرآیند همه کاره و کارآمد تولید انبوه اشکال پیچیده و قطعات پیچیده را با دقت و تکرارپذیری بالا امکان پذیر می کند.فرآیند قالب گیری تزریقی از چندین مرحله تشکیل شده است که هر کدام در تضمین تولید قطعات با کیفیت بسیار مهم هستند.بیایید مرحله به مرحله فرآیند قالب گیری تزریقی را بررسی کنیم.
مرحله 1: طراحی قالب تزریق
اولین مرحله در قالب گیری تزریقی طراحی قالب است.طراحی قالب باید عواملی مانند زاویه کشش، یکنواختی ضخامت دیوار، محل پین دروازه و اجکتور و محل قرارگیری کانال خنک کننده را در نظر بگیرد تا از کیفیت و قابلیت ساخت بهینه قطعه اطمینان حاصل شود.طراحی قالب در تعیین دقت ابعادی، پرداخت سطح و یکپارچگی ساختاری قسمت نهایی بسیار مهم است.هنگامی که طراحی قالب نهایی شد، با استفاده از فرآیندهای ماشینکاری دقیق تولید می شود.
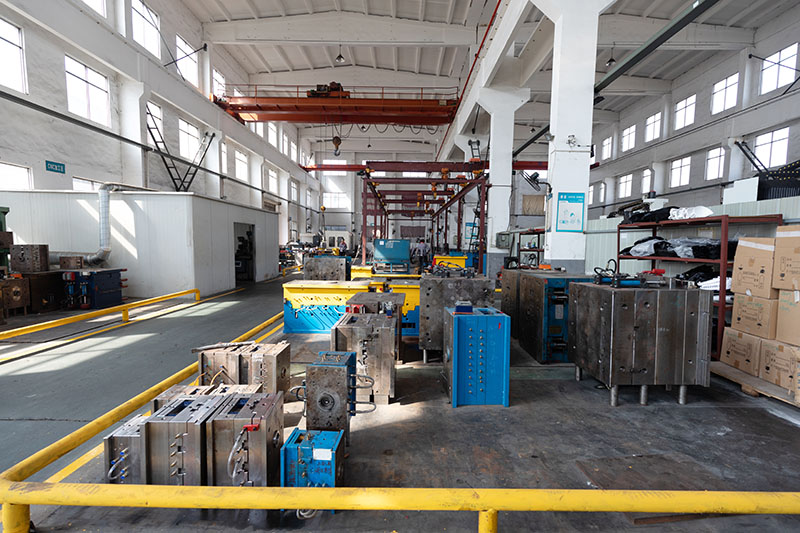
مرحله 2: آماده سازی مواد
مواد اولیه معمولاً به صورت گلوله یا گرانول بر اساس نیازهای خاص محصول نهایی با دقت انتخاب می شوند.مهم است که خواص مواد مانند جریان مذاب، ویسکوزیته، انقباض و استحکام را در نظر بگیرید تا مطمئن شوید که قطعه تمام شده دارای خواص مطلوب است.علاوه بر این، رنگها، افزودنیها یا الیاف تقویتکننده را میتوان در این مرحله برای دستیابی به عملکرد و ظاهر مطلوب در ترکیب مواد گنجاند.
مرحله 3: بستن و تزریق
پس از آماده شدن مواد و قالب، مراحل بستن و تزریق فرآیند آغاز می شود.دو نیمه قالب به طور محکم در داخل دستگاه قالب گیری تزریقی به هم متصل می شوند تا یک حفره بسته تشکیل شود.سپس رزین پلاستیکی تا دمای دقیق گرم می شود و تحت فشار بالا به داخل قالب تزریق می شود.همانطور که مواد مذاب حفره را پر می کند، شکل پیکربندی قالب را به خود می گیرد.مرحله تزریق نیاز به کنترل دقیق پارامترهای فرآیند مانند سرعت تزریق، فشار و زمان خنکسازی دارد تا از نقصهایی مانند حفرهها، علائم سینک یا تاب برداشتن جلوگیری شود.
مرحله 4: خنک سازی و انجماد
پس از پر شدن حفره، پلاستیک مذاب می تواند در داخل قالب خنک و جامد شود.خنک کاری مناسب برای دستیابی به عملکرد قطعه مورد نیاز و به حداقل رساندن زمان چرخه حیاتی است.طراحی قالب دارای کانالهای خنککننده است که به مواد کمک میکند تا گرما را به سرعت و به طور یکنواخت دفع کند و کیفیت قطعه و ثبات ابعادی ثابت را تضمین کند.نظارت و بهینه سازی فرآیند خنک سازی برای جلوگیری از مشکلاتی مانند تغییر شکل قطعه یا تنش های داخلی که می تواند یکپارچگی محصول نهایی را به خطر بیندازد، بسیار مهم است.
مرحله 5: خروج و قطعات
حذف پس از خنک شدن و جامد شدن کامل پلاستیک، قالب باز می شود و قسمت تازه تشکیل شده از حفره خارج می شود.فعال کردن پین اجکتور یا مکانیزم تعبیه شده در قالب، قطعه را به بیرون هل می دهد و آن را از سطح ابزار رها می کند.فرآیند پرتاب باید به دقت مورد توجه قرار گیرد تا از آسیب به قطعه یا قالب جلوگیری شود، به خصوص در مورد هندسه های پیچیده یا قطعات جدار نازک.سیستم های خودکار را می توان برای سرعت بخشیدن به جهش و حذف قطعات پیاده سازی کرد و به بهبود راندمان کلی تولید کمک کرد.
مرحله 6: برش و تکمیل
هنگامی که قطعه خارج شد، مواد اضافی (به نام فرز) بریده می شود یا از قطعه جدا می شود.این ممکن است شامل عملیات ثانویه مانند تخلیه، برداشتن دروازه یا هر فرآیند تکمیلی دیگری باشد که برای دستیابی به مشخصات قطعه نهایی لازم است.هر گونه نقص یا ناهماهنگی سطح برطرف می شود و بسته به نیازهای کاربردی، ممکن است قطعه پردازش اضافی مانند ماشینکاری، جوشکاری یا مونتاژ دریافت کند.
مرحله 7: کنترل کیفیت و تست
در طول فرآیند قالب گیری تزریقی، اقدامات کنترل کیفیت برای اطمینان از تولید قطعات با کیفیت بالا اجرا می شود.این ممکن است شامل نظارت و کنترل پارامترهای فرآیند، بازرسی قطعات برای عیوب، و انجام آزمایشهای مختلف برای ارزیابی دقت ابعاد، استحکام و سایر ویژگیها باشد.
به طور خلاصه، فرآیند قالب گیری تزریقی یک فناوری ساخت پیچیده و همه کاره است که قادر به تولید طیف گسترده ای از قطعات و محصولات پلاستیکی با دقت و کارایی استثنایی است.هر مرحله از فرآیند، از آمادهسازی مواد و طراحی قالب گرفته تا خنکسازی، تخلیه و کنترل کیفیت، نیازمند توجه دقیق به جزئیات و تخصص برای دستیابی به نتایج مطلوب است.با درک و بهینه سازی هر مرحله از فرآیند قالب گیری تزریقی، تولیدکنندگان می توانند به طور مداوم قطعات با کیفیت بالا و مقرون به صرفه را برای پاسخگویی به نیازهای صنایع و کاربردهای مختلف ارائه دهند.
زمان ارسال: دسامبر-12-2023