Шприцоването е широко използван производствен процес, използван за производството на различни пластмасови части и продукти.Този многостранен и ефективен процес позволява масово производство на сложни форми и сложни части с висока прецизност и повторяемост.Процесът на леене под налягане се състои от няколко стъпки, всяка от които е решаваща за осигуряване на производството на висококачествени части.Нека проучим процеса на леене под налягане стъпка по стъпка.
Стъпка 1: Дизайн на шприцформа
Първата стъпка в леенето под налягане е проектирането на формата.Дизайнът на матрицата трябва да вземе предвид фактори като ъгъл на теглене, еднаквост на дебелината на стената, местоположение на шибъра и ежекторния щифт и разположение на охлаждащия канал, за да се осигури оптимално качество на частта и технологичност.Дизайнът на формата е от решаващо значение за определяне на точността на размерите, повърхностното покритие и структурната цялост на крайната част.След като дизайнът на формата е финализиран, той се произвежда чрез прецизни процеси на обработка.
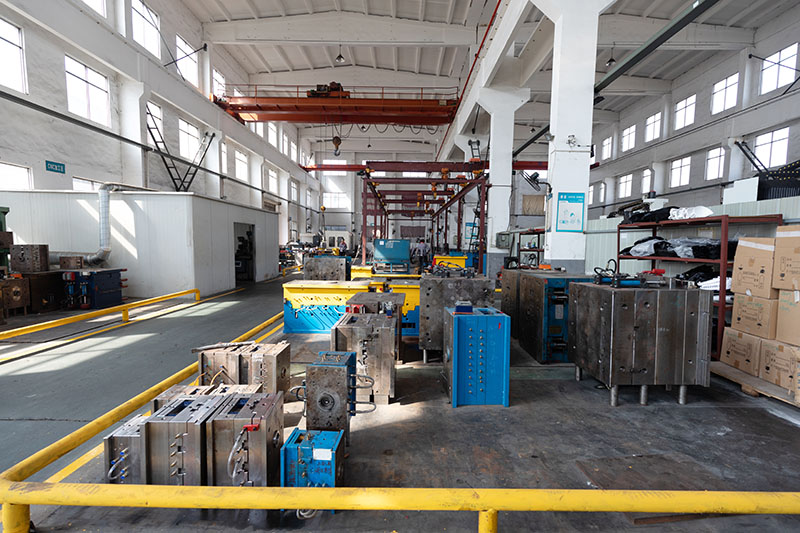
Стъпка 2: Подготовка на материала
Суровините, обикновено под формата на пелети или гранули, са внимателно подбрани въз основа на специфичните изисквания на крайния продукт.Важно е да се вземат предвид свойствата на материала като поток на стопилка, вискозитет, свиване и якост, за да се гарантира, че завършената част има желаните свойства.В допълнение, оцветители, добавки или подсилващи влакна могат да бъдат включени в сместа от материали на този етап, за да се постигне желаната производителност и външен вид.
Стъпка 3: Затягане и инжектиране
След като материалът и формата са подготвени, започват етапите на затягане и инжектиране на процеса.Двете половини на формата са здраво захванати заедно вътре в машината за леене под налягане, за да образуват затворена кухина.След това пластмасовата смола се нагрява до точна температура и се инжектира във формата под високо налягане.Докато разтопеният материал запълва кухината, той приема формата на конфигурацията на формата.Етапът на впръскване изисква внимателен контрол на параметрите на процеса като скорост на впръскване, налягане и време за охлаждане, за да се избегнат дефекти като кухини, следи от потъване или изкривяване.
Стъпка 4: Охлаждане и втвърдяване
След като кухината се запълни, разтопената пластмаса може да се охлади и втвърди във формата.Правилното охлаждане е от решаващо значение за постигане на необходимата производителност на частта и минимизиране на времената на цикъла.Дизайнът на матрицата включва охлаждащи канали, които помагат на материала да разсейва топлината бързо и равномерно, осигурявайки постоянно качество на детайла и стабилност на размерите.Наблюдението и оптимизирането на процеса на охлаждане е от решаващо значение за предотвратяване на проблеми като деформация на части или вътрешни напрежения, които могат да компрометират целостта на крайния продукт.
Стъпка 5: Изваждане и части
Отстраняване След като пластмасата е напълно охладена и втвърдена, матрицата се отваря и новоформираната част се изхвърля от кухината.Активирането на ежекторен щифт или механизъм, вграден във формата, избутва детайла навън, освобождавайки го от повърхността на инструмента.Процесът на изхвърляне трябва да бъде внимателно обмислен, за да се предотврати повреда на частта или формата, особено при сложни геометрии или тънкостенни части.Могат да бъдат внедрени автоматизирани системи за ускоряване на изхвърлянето и премахването на части, което спомага за подобряване на цялостната производствена ефективност.
Стъпка 6: Подстригване и завършване
След като частта бъде изхвърлена, всеки излишен материал (наречен грапавини) се подрязва или отстранява от частта.Това може да включва второстепенни операции, като премахване на ръбове, премахване на врата или всеки друг довършителен процес, необходим за постигане на окончателните спецификации на частта.Всички повърхностни несъвършенства или несъответствия се разглеждат и в зависимост от изискванията на приложението частта може да получи допълнителна обработка, като механична обработка, заваряване или сглобяване.
Стъпка 7: Контрол на качеството и тестване
По време на процеса на леене под налягане се прилагат мерки за контрол на качеството, за да се гарантира производството на висококачествени части.Това може да включва наблюдение и контрол на параметрите на процеса, проверка на частите за дефекти и провеждане на различни тестове за оценка на точността на размерите, здравината и други свойства.
В обобщение, процесът на леене под налягане е сложна и многофункционална производствена технология, способна да произвежда широка гама от пластмасови части и продукти с изключителна прецизност и ефективност.Всяка стъпка в процеса, от подготовката на материала и дизайна на матрицата до охлаждането, изхвърлянето и контрола на качеството, изисква внимателно внимание към детайла и опит за постигане на оптимални резултати.Чрез разбиране и оптимизиране на всеки етап от процеса на леене под налягане, производителите могат постоянно да доставят висококачествени, рентабилни части, за да отговорят на нуждите на различни индустрии и приложения.
Време на публикуване: 12 декември 2023 г