The automotive industry continues to evolve, as does the demand for high-quality, reliable and cost-effective car components. Automotive Injection Molding is considered as an outstanding contribution to the automotive industry. This process plays a vital role in meeting the industry's stringent requirements for precision, strength and efficiency.
In this article, we will take a closer look at the importance of injection molding in the automotive industry, its impact on automotive parts production, and how it is reshaping the manufacturing landscape.
- Automotive Injection Molding Overview
Automotive injection molding is a manufacturing technique that uses a high-pressure plastic injection to form a variety of automotive parts, such as bumpers, fenders, dashboards, door panels, headlights, etc. It is one of the most common methods for the mass production of plastic parts.
In the early years of the automotive industry, plastic injection molding technology was not widely used. At that time, cars were almost entirely made of metal. These metal parts were clunky, heavy and expensive. However, as the automotive industry grew, so did the need for more efficient and cost-effective manufacturing methods. Therefore, automakers began to experiment with the use of plastic car parts in production. The adoption of injection molding has significantly impacted on manufacturing automotive parts, as it allows for fast, accurate and economical mass production.
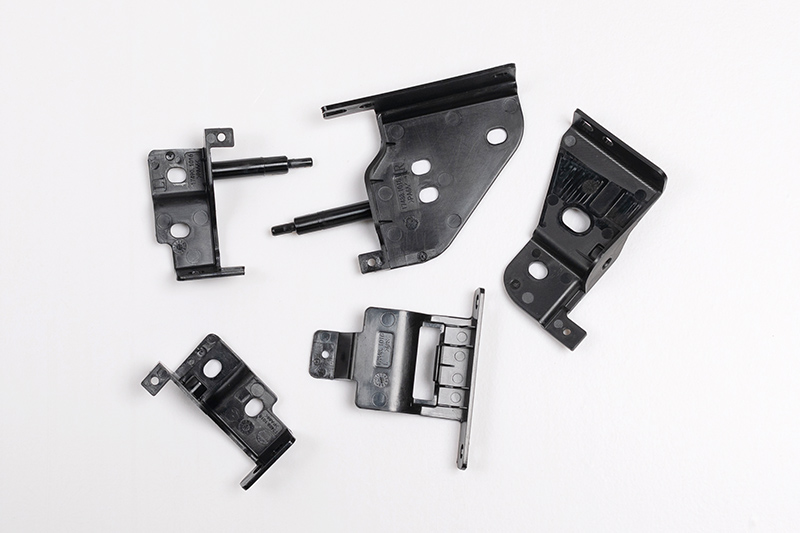
- Advantages of Injection Molding for Automotive Applications
Here are a few reasons why this process is beneficial for producing automotive plastic parts and components.
1. Cost-effectiveness
Injection molding enables the production of complex parts with minimal material waste, making it a cost-effective solution for automotive manufacturers. The high level of automation in injection molding also helps reduce labor costs and improve production efficiency.
2. Accuracy and Repeatability
Auto parts need to meet strict quality standards to ensure safety and performance. Injection molding produces car parts with exceptional precision and consistency, eliminating variations common in traditional manufacturing methods. This precision is critical for components such as interior panels, dashboard trim and precision machined parts.
3. Material Availability
Injection molding supports a wide range of materials, such as PP, PC, ABS, TPE, Nylon, and more, allowing flexibility in material selection based on specific part requirements. This versatility enables the production of automotive parts with different properties (such as impact resistance, heat resistance and surface finish) to meet the diverse needs of the industry.
4. Color Options
In injection molding for the automotive industry, the color of molded car parts can be easily modified to match the color scheme of the car. Unlike other processes, injection molding allows the color to be mixed with the raw material prior to production. This eliminates the need for coloring after the molding process is complete.
5. Design Flexibility
The design flexibility offered by injection molding is critical to the automotive industry, where complex part designs are common. With advanced mold design and processing technology, injection molding helps produce automotive parts with complex shapes, undercuts, and fine details. This capability allows for greater design freedom and the integration of functional features into the part itself, improving overall performance and aesthetics.
- Future Trends and Innovations
As automotive technology continues to advance, so does the role of injection molding in shaping the future of automotive parts production. Several emerging trends and innovations are expected to further enhance the automotive industry's injection molding capabilities.
1. Advanced Materials and Composites
The combination of advanced materials and composites in the production of automotive parts brings new opportunities for injection molding. Lightweight materials, reinforced polymers and sustainable alternatives are being integrated into injection molding processes to meet the industry’s changing needs for fuel efficiency, durability and sustainability.
2. Additive Manufacturing Integration
The integration of additive manufacturing, such as 3D printing, with injection molding processes provides new avenues for rapid prototyping, mold development and the production of highly customized automotive parts. This synergy between additive manufacturing and injection molding opens up the possibility for on-demand part production and design iteration, driving innovation in the automotive industry.
3. Smart Manufacturing and Industry 4.0
The adoption of smart manufacturing principles and Industry 4.0 technologies, such as IoT machinery, data analytics and automated quality control systems, will further improve the efficiency, productivity and traceability of the injection molding process in automotive manufacturing. Real-time data insights and predictive maintenance capabilities will help minimize downtime and optimize production cycles.
In conclusion, injection molding has become a cornerstone of automotive component production, offering an effective combination of precision, flexibility and efficiency. Injection molding’s ability to produce high-quality, complex parts while remaining cost-effective has made it a driving force in the automotive industry. As technology continues to advance and materials become more sophisticated, the role of injection molding in automotive manufacturing will continue to expand, shaping the future of automotive parts production and driving innovation across the industry.
Post time: Jan-22-2024